-
Products
- Products
- Fire resistant cables
- Power cables 1-145 kV
- Building cables
- Pre-wired installation cables in conduits
-
Specialty LV cables and flexible cords
- Overview
- TITANEX® H07RN-F 450/750 V
- H03V2V2-F (RKK 90) 300/300 V
- H03VVH2-F (SKX-U) 300/300 V
- H05V2V2-F (RKK-S 90GR) 300/500 V
- H05VVH2-F (RKX) 300/500 V
- H05VV-F (RKK) 300/500 V
- H03V2V2H2-F (SKX-U 90GR) 300/300 V
- H03VV-F (SKK) 300/300 V
- PUREAX (H07BQ-F)
- RKX 90
- S03Z1Z1H2-F (SQX) 300/300 V
- H05Z1Z1-F (RQQ) 300/500 V
- Robotic lawnmower wire H05Z1-K (RQ) Tinned 300/500 V
- NOAC-E HFFR 300/500 V (S05Z1A7Z1-F)
- Telecom - LAN - security
- Industrial cabling
- Accessories
- Your business
- News
- Support and Tools
- We are Nexans
- Sustainability at Nexans
- Search
- Contact us
- Compare
- Sign in
Innovation
Floating offshore wind
Dec 9, 2022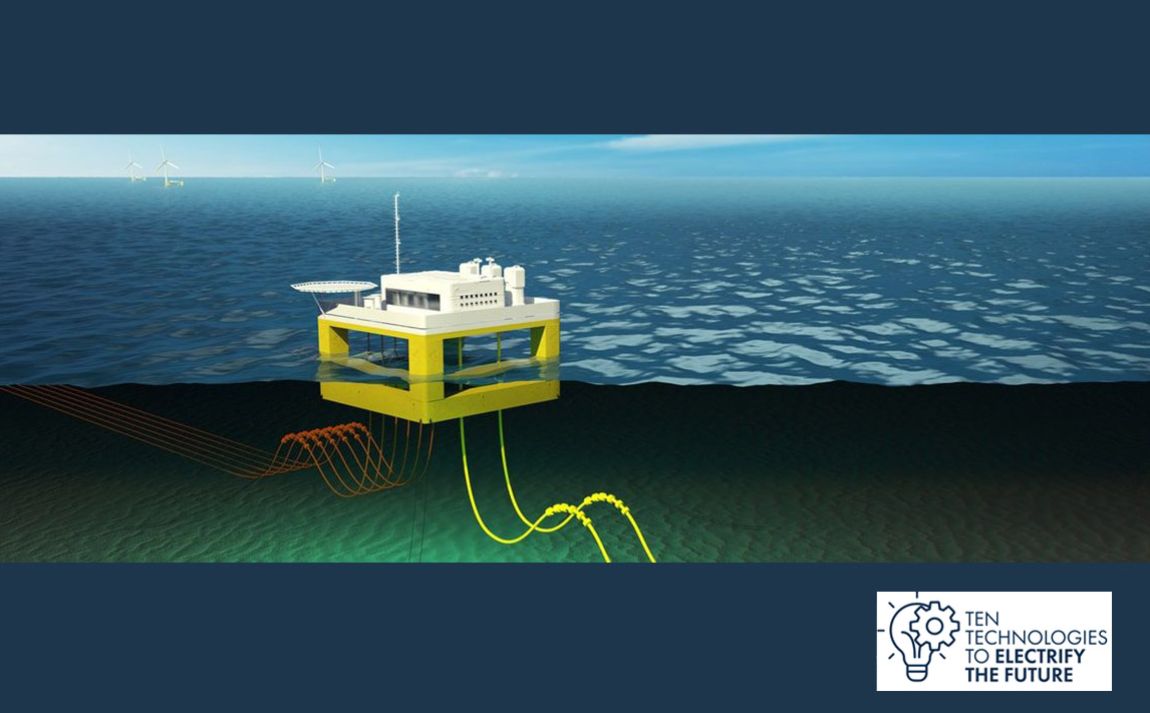
Winds of change
Turbine technology has made huge strides since the first wind farms appeared in our oceans more than twenty years ago. Today’s turbines are bigger and more efficient than ever, with rotor diameters in excess of 200 metres and power ratings of 10 MW and more. These advances have played a critical part in driving down the cost of offshore wind.
Almost every offshore wind turbine in existence today depends on bottom-fixed foundations, which are a good solution in relatively shallow waters – those up to 60 metres deep. These foundations are steel and concrete footings that attach the turbine structure directly to the seabed.
The vast majority of oceans and seas have waters that exceed 60 metres in depth – and this is where the highest and most consistent winds are found. In Europe, for example, 80% of the wind resource occurs over waters with a depth of 60 metres or more. Conventional foundations are not cost effective in these situations. So there are large areas where wind resources are untapped.
New horizons for offshore wind
Floating wind turbines overcome the problem of providing foundations in deep water. Instead of being rooted to the seabed, turbines are mounted on a floating substructure that is tethered with mooring lines and anchors.
All of this is a game changer for offshore wind. Rather than being restricted to a depth of 60 metres, floating turbines can be deployed in waters up to 1000 metres deep – and potentially much more.
This has exciting potential to expand the geographical reach of offshore wind. The northern part of the North Sea basin is one example. The depth of waters here typically far exceeds 60 metres, putting them beyond the reach of conventional foundations.
Hywind Scotland in the UK – the world’s first floating wind farm – highlights what can be achieved. Sited about 30 km offshore in waters up to 120 metres deep, Hywind has been in service successfully since 2017. Hywind has the highest capacity factor for any wind farm in the UK: in 2020, it set a new UK record, achieving an average capacity factor of 57.1%. This compares to an offshore wind average in the UK of about 40%.
The technology behind floating wind is set to have an impact far beyond the North Sea, particularly in geographies where the sea gets very deep, very near the shore. Examples include the Mediterranean basin, the west coast of the United States, South Korea and Japan – all of which have huge offshore wind resources waiting to be tapped. Floating wind can also be deployed in shallow waters where seabed conditions prevent the use of conventional foundations.
Making floating wind a reality
Currently, floating wind accounts for just 0.1% of the offshore wind total. But that is set to change. Forecasts by the Global Wind Energy Council suggest that by 2030, floating wind could account for 6.1% of all new installations with an estimated 16.5 GW of new capacity added within the next ten years. Robust, cost-effective technologies hold the key to achieving this.
One of the big technical challenges with floating offshore wind is exporting the electricity they generate. There are three factors in play. First, cable links between wind farms and the shore are longer because turbines are typically sited further out to sea. Second, the power levels that must be handled are increasing as turbines grow in size. Third – and most importantly – dynamic cables are required. These must be capable of accommodating movements of the floater structure caused by currents, tides and wind. Resilience is critical.
Smarter dynamic cables
Nexans’ track record in high-voltage submarine cable systems and dynamic cables means the company is ideally placed to support the development of floating wind. Indeed, Nexans supplied dynamic cables for the Hywind Demo and Hywind Scotland floating wind projects. The company’s experience has deep roots: Nexans developed its first dynamic cable back in 1983.
Today, the innovation continues. The focus is now on developing HV dynamic cables that can handle more power and greater voltages than ever before. This new generation of cables will be lighter and more flexible than traditional subsea cables. They will also be smarter, thanks to the integration of optical fibre elements to provide real-time monitoring – providing critical information on various parameters of the cables and ensuring years of reliable operation.
Links:
Our websites
Select your country to find our products and solutions
-
Africa
- Africa
- Ghana
- Ivory Coast
- Morocco
- North West Africa
- Americas
- Asia
- Europe
- Oceania